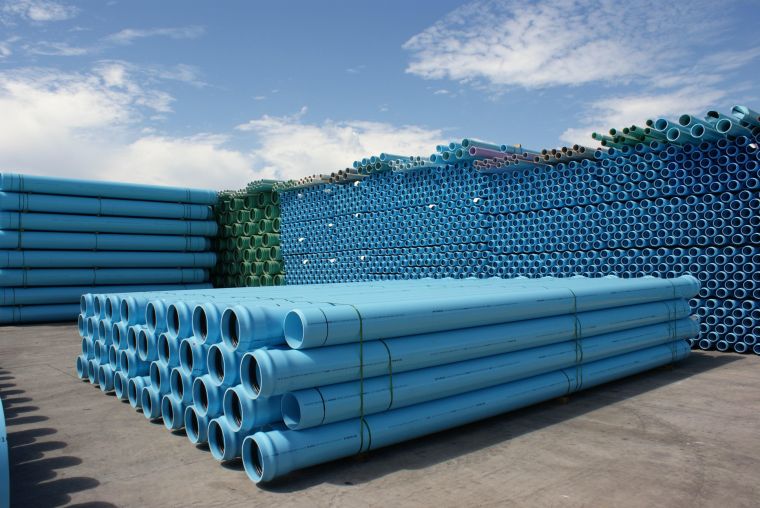
What is PVC (PolyVinyl Chloride)?
Polyvinyl Chloride (PVC or Vinyl) is an economical and versatile thermoplastic polymer widely used in building and construction industry to produce door and window profiles, pipes (drinking and wastewater), wire and cable insulation, medical devices, etc. It is the world’s third largest thermoplastic material by volume after polyethylene and polypropylene.
It is a white, brittle solid material available in powder form or granules. Due to its versatile properties, such as lightweight, durable, low cost and easy processability, PVC is now replacing traditional building materials like wood, metal, concrete, rubber, ceramics, etc. in several applications.
Some of the key suppliers of PVC are:
- Sylvin Technologies
- Teknor Apex
- Colorite Compounds (Tekni-Plex)
- Inovyn
- Ineos
- SABIC
Basic Forms of PVC
Polyvinyl Chloride is widely available in two broad categories: Flexible and Rigid. But, there are more types like CPVC, PVC-O and PVC-M.
-
- Plasticized or Flexible PVC (Density: 1.1-1.35 g/cm3): Flexible PVC is formed by the addition of compatible plasticizers to PVC which lower the crystallinity. These plasticizers act like lubricants resulting in a much clearer and flexible plastic. This type of PVC is sometimes called as PVC-P.
-
- Unplasticized or Rigid PVC (Density: 1.3-1.45 g/cm3): It is a stiff and cost-effective plastic with high resistance to impact, water, weather, chemicals and corrosive environments. This type of PVC is also known as UPVC, PVC-U or uPVC.
-
- Chlorinated Polyvinyl Chloride or perchlorovinyl: It is prepared by chlorination of PVC resin. High chlorine content imparts high durability, chemical stability and flame retardancy. CPVC can withstand a wider range of temperatures.
-
- Molecular Oriented PVC or PVC-O: It is formed by reorganizing the amorphous structure of PVC-U into a layered structured. Bi-axially oriented PVC has enhanced physical characteristics (stiffness, fatigue resistance, lightweight, etc.).
- Modified PVC or PVC-M: It is an alloy of PVC formed by addition of modifying agents, resulting in enhanced toughness and impact properties.
Key Facts About Rigid and Flexible PVC
Strengths | Limitations |
Rigid PVC | |
|
|
Flexible PVC | |
|
|
Chlorinated PVC (CPVC)
CPVC is manufactured by chlorination of PVC polymer thereby raising the chlorine content from 56% to around 66%.
Chlorination of PVC reduces the forces of attraction between the molecular chains. CPVC is also essentially amorphous. Both of these factors allow CPVC to be stretched more easily and to a greater extent than PVC above its glass transition temperature, Tg. Pipe (436), moldings (376) and sheet are formulated for high temperature use based on CPVC or blends of CPVC and PVC.
How is PVC manufactured?
Vinyl chloride monomer (VCM) is produced from the chlorination of ethylene and pyrolysis of the resulting ethylene dichloride (EDC) in a cracking unit. PVC (glass transition temperature: 70-80°C) is produced by polymerization of vinyl chloride monomer (VCM).
![]() Molecular Formula of Vinyl Chloride C2H3Cl |
Addition Polymerization ![]() |
![]() Molecular Formula of Polyvinyl Chloride (C2H3Cl)n |
The popular methods used to manufacture PVC commercially are:
- Suspension PVC (S-PVC)
- Bulk or Emulsion (E-PVC)
Suspension PVC (S-PVC) Process
In pressure-tight reactor, the monomer is introduced with polymerization initiator and other additives. The content of the reaction vessel are mixed continuously to maintain suspension and ensure uniform particle size of PVC resin.
Typical suspension polymerized PVC has a mean particle size of 100-150 µm with a range of 50-250 µm.
S-PVC grades are formulated to meet an extensive range of requirements such as, high plasticizer absorption for flexible products, or high bulk density and good powder flow required for rigid extrusion
Bulk or Emulsion (E-PVC) Process
In this process, surfactants (soaps) are used to disperse the vinyl chloride monomer in water. The monomer is trapped inside soap micelles are protected by the soap and polymerization takes place using water soluble initiators.
The primary particles are solid, smooth surfaced spheres which are clustered into irregular shaped aggregates with a typical mean particle size of 40-50 µm with a range of 0.1-100 µm.
E-PVC resins are used in a wide range of specialty applications such as coating, dipping or spreading.
Suspension PVC (S-PVC) Process | Bulk or Emulsion (E-PVC) Process |
|
|
Key Properties of PVC Polymer
PVC is a very versatile and cost-effective material. Its main properties and benefits include:
-
- Electrical Properties: PVC is a good insulation material, thanks to its good dielectric strength.
-
- Durability: PVC is resistant to weathering, chemical rotting, corrosion, shock and abrasion. It is therefore the preferred choice for many long-life and outdoor products.
-
- Flame Retardancy: Because of its high chlorine content, PVC products are self- extinguishing. Its oxidation index is ≥45. Antimony trioxide has been used extensively, usually in combination with phosphate ester plasticizers, giving excellent fire performance and mechanical properties.
-
- Cost/Performance Ratio: PVC has good physical as well as mechanical properties and provides excellent cost-performance advantages. It has long life span and need low maintenance.
-
- Mechanical Properties: PVC is abrasion-resistant, lightweight and tough.
- Chemical Resistance: PVC is resistant to all inorganic chemicals. It has very good resistance against diluted acids, diluted alkalis and aliphatic hydrocarbons. Attacked by ketones; some grades swollen or attacked by chlorinated and aromatic hydrocarbons, esters, some aromatic ethers and amines, and nitro- compounds
Methods to Enhance PVC Properties – Role of Additives
PVC resin obtained from polymerization is extremely unstable due to its low thermal stability & high melt viscosity. It needs to be modified before processing into finished products. Its properties can be enhanced/modified by adding several additives, such as heat stabilizers, UV stabilizers, plasticizers, impact modifiers, fillers, flame retardants, pigments, etc.
Selection of these additives to enhance polymer’s properties is dependent on end application requirement. For example:
-
- Plasticizers (Phthalates, Adipates, Trimellitate, etc.) are used as softening agents to enhance rheological as well mechanical performance (toughness, strength) of vinyl products by raising the temperature. Factors that affect the selection of plasticizers for vinyl polymer are:
- Polymer Compatibility
- Low Volatility
- Cost
Flexible PVC Pipe
- Plasticizers (Phthalates, Adipates, Trimellitate, etc.) are used as softening agents to enhance rheological as well mechanical performance (toughness, strength) of vinyl products by raising the temperature. Factors that affect the selection of plasticizers for vinyl polymer are:
-
- PVC has a very low thermal stability and stabilizers help prevent degradation of polymer during processing or exposure to light. When subjected to heat, vinyl compounds initiate a self-accelerating dehydrochlorination reaction and these stabilizers neutralize the HCl produced enhancing the life of polymer. Factors to be considered while selecting heat stabilizer are:
- Technical requirements
- Regulatory Approval
- Cost
- PVC has a very low thermal stability and stabilizers help prevent degradation of polymer during processing or exposure to light. When subjected to heat, vinyl compounds initiate a self-accelerating dehydrochlorination reaction and these stabilizers neutralize the HCl produced enhancing the life of polymer. Factors to be considered while selecting heat stabilizer are:
-
- Fillers are added in PVC compounds for a variety of reasons. Today, a filler can be a true performance additive by delivering value in new and interesting ways at the lowest possible formulation cost. They help to:
- Increase stiffness and strength
- Improve impact performance
- Add color, opacity and conductivity
- And more
Calcium carbonate, titanium dioxide, calcined clay, glass, talc etc. are common types of fillers used in PVC.
- Fillers are added in PVC compounds for a variety of reasons. Today, a filler can be a true performance additive by delivering value in new and interesting ways at the lowest possible formulation cost. They help to:
-
- External lubricants are used to assist smooth passage of PVC melt through processing equipment. while internal lubricants reduce melt viscosity, prevent overheating and ensure good color of product
- Other additives like processing aids, impact modifiers, are added to enhance mechanical as well as surface properties of PVC
PVC Blend with Other Thermoplastics
PVC/Polyester Blends – These blends combine superior physical properties of polyesters with the excellent processing characteristics of PVC. Benefits include abrasion resistance, tensile properties and tear resistance.
PVC/PU Blends – These blends offer increased abrasion and chemical resistance. Some TPUs are biocompatible and when blended with PVC results in valuable products for PVC industry
PVC/NBR Blends – Flexible PVC modified with NBR are melt processable yet possess good elasticity/recovery characteristics
PVC/Polyolefin Rubber Alloys – They have potential utility in many applications where conventional flexible vinyl compounds do not meet certain end-use performance requirements.
Limitations of Polyvinyl Chloride
- Poor heat stability
- Properties can change with time, due to plasticizer migration
- Flexible PVC has lower chemical resistance than rigid PVC
- Rigid PVC has low continuous service temperature of 50°C
Applications of PVC Resin
Commercially, PVC is one of the most important thermoplastics in the world today. Rigid (unplasticized) PVC is one of the most widely used plastic materials. Main applications of both types of PVC (rigid and flexible) include:

Application | Rigid PVC | Flexible PVC |
Construction | Window Frames, Pipes, House Siding, Ports, Roofing | Waterproof Membranes, Cable Insulations, Roof Lining, Greenhouses |
Domestic | Curtain Rails, Drawer Sides, Laminates, Audio and Videotape Cases, Records | Flooring, Wall Coverings, Shower Curtains, Leather Cloth, Hosepipes |
Packaging | Bottles, Blister Packs, Transparent Packs and Punnets | Cling Film |
Transport | Car Seat Backs | Under Seal, Roof Linings, Leather Cloth Upholstery, Wiring Insulation, Window Seals, Decorative Trim |
Medical | – | Oxygen Tents, Bags And Tubing For Blood Transfusions, Drips and Dialysis Liquids |
Clothing | Safety Equipment | Waterproofs for Fishermen and Emergency Services, Life-Jackets, Shoes, Wellington Boots, Aprons and Baby Pants |
Electrical | Insulation pipes, Jacketing, Electricity Distribution Boxes, Switches, Transparent Distributor Box Housings, Plug Housings & Battery Terminals | Cable & Wire insulation, plugs, cable jackets, sockets, Sable Heads and Distributors |
Others | Floppy-Disk Covers, Credit Cards, Traffic Signs | Conveyor Belts, Inflatables, Sports Goods, Toys, Garden Hoses |
Processing of Vinyl Plastic
Some of the main processes include extrusion, calendering, injection molding, stretch blow molding, etc.
The intimate mixing of the PVC resin with its associated additives is necessary prior to converting into a thermoplastic melt. Thermal stabilization is required for processing rigid PVC, otherwise material may decompose during processing. Also, spray, blush & peel are very common molding defects associated with rigid PVC.
PVC is sensitive to the thermal history and the window of processing temperatures is quite small. Drying before processing is highly recommended, moisture rate should be lower than 0.3%.
Drying before processing is highly recommended for plasticized PVC, moisture rate should be lower than 0.3%.
Plasticized PVC | Rigid PVC |
Injection Molding |
|
|
|
Extrusion |
|
|
PVC and 3D Printing
PVC has largely been overlooked as being suitable for 3D printing, and the new developments are opening the way for PVC into the growing world of additive manufacturing. For example, Chemson Pacific Pty Ltd, a Vinyl Council of Australia member, demonstrated a world-first for 3DVinyl™ PVC material by 3D printing a giant flower vase using a pellet-fed 3D-printer.
Bonding Methods for PVC
PVC material can be bonded using different joining techniques to fabricate PVC into the finished article. All welding techniques involve the application or generation of heat to soften the material whilst pressure is applied simultaneously. Bonding techniques, involving adhesives, are also common.
Recyclability and Toxicity of PVC
Products made from PVC are 100% recyclable and can be identified as recycling code #3.

Adopting an appropriate recycling pathway for PVC is of both an economic value and an environmental benefit. Key methods for PVC recycling include:
-
- Mechanical Recycling – Mechanical recycling refers to recycling processes where PVC waste is treated through shredding, sieving and grinding. Depending on the composition, the quality of the recyclates can vary a lot. After mechanical separation, grinding, washing and treatment to eliminate impurities, it is reprocessed using various techniques (granulated or powder) and reused in the production. “High quality” can be re-used in the same types of applications, whereas “low quality” recyclates from can only be used into products made from other material.
-
- Chemical Recycling – Chemical recycling processes break up polymer into monomers (used to produce new polymers) or other substances (used as starting materials in processes of the basic chemical industry. The Chlorine is set free in the form of HCl that can be re-used or neutralized to form various products. Stabilizers containing heavy metals mostly end up in solid residues that will most probably have to be landfilled.
- Feedstock Recycling – It involves (usually) thermal treatment of the PVC waste stream with recovery of hydrogen chloride that can then be returned to the PVC production process or used in other processes.

Recycled PVC can be used to produce packaging, film and sheet, loose-leaf binders, pipes, carpet backing, electrical boxes, cables and more.
The industry is working with the regulatory authorities to ensure that recycling activities remain sustainable while complying with the regulatory regime.
Presence of chlorine content and use of additives such as plasticizers bought PVC under scrutiny for a number of years. Concerns have been raised at regular intervals, in several regions, regarding the possible negative impact of phthalates on the environment and human health. However, on further investigations and studies certain phthalates are now confirmed safe for use in current applications.
Similarly, Europe has phased out use of lead-based stabilizers in vinyl compounds due to their classification as reprotoxic, harmful, dangerous for the environment and their presence (heavy metal) causing issues in waste management strategies.
Recycling Initiatives in the PVC Industry
US
Vinyl (PVC) Institute is one of the premier organizations representing the leading manufacturers of vinyl, vinyl chloride monomer, and vinyl additives and modifiers in US.
Recently, it has launched a new initiative ‘+Vantage Vinyl’ to advance sustainability efforts throughout the vinyl industry. It engages companies across the entire vinyl value chain from raw material manufacturers and suppliers to final product manufacturers
Europe
Recycling now being a key to circular economy, the European PVC industry is no behind in contributing to the circular economy goals.
Recovinyl, as an industry-wide recycling platform, is gathering recyclers and converters from all over Europe. Recovinyl is an initiative by the European PVC value-chain aimed at facilitating PVC waste collection and recycling. The scheme is funded by VinylPlus, the voluntary commitment to sustainable development by the European PVC Industry (originally funded through the Vinyl 2010 initiative).
Australia
Vinyl Council of Australia represents the PVC/vinyl value chain in Australia. It closely follows Europe’s VinylPlus program. With its own PVC Stewardship Program, Vinyl Council of Australia aims to enable raw material suppliers, products manufacturers and distributors to be joint stewards of the safe and beneficial production, use and disposal of PVC products.
Canada
The Vinyl Institute of Canada and FEPAC, Quebec’s leading plastics association, offer Eco Responsible, a sustainability management certification program for manufacturers in the vinyl industry, and for any other organizations in the plastics industry across Canada.
Bio-based PVC Developments
Developing plastics from soy, wheat, or even sugarcane is not new. Now, like several other polymers, advancement in bio-based PVC formulations or even produce bio-based PVC resins is gaining momentum. Two industry players – Ineos and Vynova – have developed bio-PVCs based on renewable ethylene feedstock derived from non-food chain-based biomass.
Properties Comparison: Flexible PVC vs. Rigid PVC
Keeping information about the properties of a thermoplastic beforehand is always beneficial. This helps in selecting the right engineering thermoplastic for a particular application. It also assists in evaluating if the end use requirement would be fulfilled or not.
The table below comprises of all relevant properties of Flexible PVC and Rigid PVC. From physical properties, dimensional stability, electrical performances to fire and thermal properties, find out every possible attribute with its values here.
Property | Plasticized (Flexible) PVC | Unplasticized (Rigid) PVC |
Dimensional Stability | ||
Coefficient of Linear Thermal Expansion | 5–20 x 10-5 /°C | 5–18 x 10-5 /°C |
Shrinkage | 0.2–4% | 0.1–0.6% |
Water Absorption 24 hours | 0.2–1% | 0.04–0.4% |
Electrical Performances | ||
Arc Resistance | – | 60–80sec |
Dielectric Constant | 3–5 | 3–4 |
Dielectric Strength | 10–30kV/mm | 10–40kV/mm |
Dissipation Factor | 400–1600 x 10-4 | 60–200 x 10-4 |
Volume Resistivity | 10–16 x 1015 Ohm.cm | 15–16 x 1015 Ohm.cm |
Fire Performances |
||
Fire Resistance (LOI) | 20–40% | 40–45% |
Flammability UL94 | HB | V0 |
Mechanical Properties | ||
Elongation at Break | 100–400% | 25–80% |
Flexibility (Flexural Modulus) | 0.001–1.8GPa | 2.1–3.5GPa |
Hardness Rockwell M | 1 | 1–70 |
Hardness Shore D | 15–70 | 65–90 |
Stiffness (Flexural Modulus) | 0.001–1.8GPa | 2.1–3.5GPa |
Strength at Break (Tensile) | 7–25MPa | 35–60MPa |
Strength at Yield (Tensile) | 4–7MPa | 35–50MPa |
Toughness (Notched Izod Impact at Room Temperature) | – | 20–110J/m |
Young Modulus | 0.001–1.8GPa | 2.4–4GPa |
Optical Properties | ||
Haze | 3–5% | – |
Transparency (% Visible Light Transmission) | 75–85% | 80% |
Physical Properties | ||
Density | 1.3–1.7g/cm3 | 1.35–1.5g/cm3 |
Glass Transition Temperature | -50–-5°C | 60–100°C |
Radiation Resistance | ||
UV Light Resistance | Fair | Fair |
Service Temperature | ||
Ductile / Brittle Transition Temperature | -40–-5°C | -10–1°C |
HDT @0.46 Mpa (67 psi) | 30–56°C | 57–80°C |
HDT @1.8 Mpa (264 psi) | 30–53°C | 54–75°C |
Max Continuous Service Temperature | 50–80°C | 50–80°C |
Min Continuous Service Temperature | -40–-5°C | -10–1°C |
Others | ||
Sterilization Resistance (Repeated) | Poor | – |
Thermal Insulation (Thermal Conductivity) | 0.16W/m.K | 0.16W/m.K |
Chemical Resistance | ||
Acetone ![]() |
Non Satisfactory | |
Ammonium hydroxide @ 30%, ![]() |
Satisfactory | |
Ammonium hydroxide @ diluted, ![]() |
Satisfactory | |
Ammonium hydroxide @ diluted, 60°C | Limited | |
Aromatic hydrocarbons @ ![]() |
Non Satisfactory | |
Aromatic hydrocarbons @ hot conditions | Non Satisfactory | |
Benzene ![]() |
Non Satisfactory | |
Butylacetate ![]() |
Non Satisfactory | |
Butylacetate @ 100%, 60°C | Non Satisfactory | |
Chlorinated solvents @ ![]() |
Non Satisfactory | |
Chloroform @ ![]() |
Non Satisfactory | |
Dioctylphtalate @ 100%, 100°C | Non Satisfactory | |
Dioctylphtalate ![]() |
Non Satisfactory | |
Dioctylphtalate @ 100%, 60°C | Non Satisfactory | |
Ethanol @ 96%, ![]() |
Non Satisfactory | Satisfactory |
Ethyleneglycol (Ethane diol) @ 100%, 100°C | Non Satisfactory | |
Ethyleneglycol (Ethane diol) ![]() |
Satisfactory | |
Ethyleneglycol (Ethane diol) @ 100%, 50°C | Satisfactory | |
Glycerol ![]() |
Satisfactory | |
Hydrogen peroxide @ 30%, 60°C | Satisfactory | |
Kerosene @ ![]() |
Satisfactory | |
Methanol ![]() |
Satisfactory | |
Methylethyl ketone ![]() |
Non Satisfactory | |
Mineral oil @ ![]() |
Satisfying | |
Phenol @ ![]() |
Limited | |
Soap @ ![]() |
Satisfying | |
Soap @ 60°C | Limited | |
Sodium hydroxide @ <40%,> | Satisfying | |
Sodium hydroxide @ <40%,> | Limited | |
Sodium hydroxide @ 10%, ![]() |
Satisfying | |
Sodium hydroxide @ 10%, 90°C | Non Satisfactory | |
Sodium hypochlorite @ 20%, ![]() |
Satisfying | |
Strong acids @ concentrated, ![]() |
||
Toluene @ ![]() |
Non Satisfactory | |
Toluene @ 60°C | ||
Xylene @ ![]() |